In the dynamic and competitive landscape of today's business world, the pursuit of efficiency and continuous improvement stands as a cornerstone for sustainable success. As businesses navigate through challenges such as individualized quality expectations, price and product competition, time constraints, and rapidly evolving customer demands, the need for streamlined processes and waste reduction becomes more critical than ever.
Lean methodologies, originating from the post-World War II era and maturing through the Toyota Production System in Japan, have become synonymous with excellence in manufacturing and beyond. The Lean approach aims to eliminate waste, focus on customer value, and cultivate a mindset of continuous improvement.
Non-Value-Adding Activities: 3M
- Muda: Overproduction, Waiting, Transportation, Overprocessing, Inventory, Motion, Defects, Underutilized Talent
- Mura: Irregular Workload, Unstable Processes, Quantity Fluctuations
- Muri: Overloading Machines, People, or Processes, Capacity Overload
Understanding and eliminating these non-value-adding activities is crucial for organizations aiming to streamline processes, reduce waste, and enhance overall efficiency in line with Lean principles.
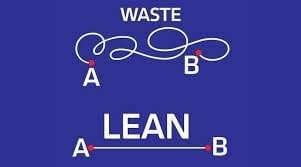
In the words of Taichi Ohno, the visionary behind the Toyota Production System,
"Our primary responsibility is to scrutinize the timeline, starting from the moment a customer places an order to the point of cash collection, with the objective of eliminating any inefficiencies that do not contribute value, thereby reducing the overall time involved.''
Integration of Technology in Lean: Google’s CEO has called AI more profound than fire or electricity. AI has the potential to enhance Lean processes by automating routine tasks, providing valuable insights through data analytics, and facilitating quicker decision-making.
How IoT Sensors are Revolutionizing Precision Agriculture
The evolution of agriculture over the last century and a half has been marked by the transformative power of mechanization and biotechnology. Today, we stand on the brink of a new era – precision agriculture.
The sensors act as innumerable miniature eyes and ears dispersed across fields, perpetually observing and listening to the environment. Embedded in devices, they monitor crucial factors like soil moisture, temperature, humidity, and nutrient levels. The data collected is transmitted to a centralized platform for processing and analysis, turning farmers into data-driven decision-makers.
- Reduced waste of inputs, such as water and fertilizers, translates to lower operational costs and increased profitability. This commitment paves the path to prosperity for both farmers and the agricultural sector as a whole, aligning seamlessly with the principles of Lean philosophy.
John Deere Turns To 3D Printing More Efficient Engine Parts
John Deere, a global leader in agricultural equipment, is breaking new ground by incorporating metal 3D-printed engine parts into its tractors (2020, Germany). This move isn't just about staying on the cutting edge; it's about efficiency and cost-effectiveness.
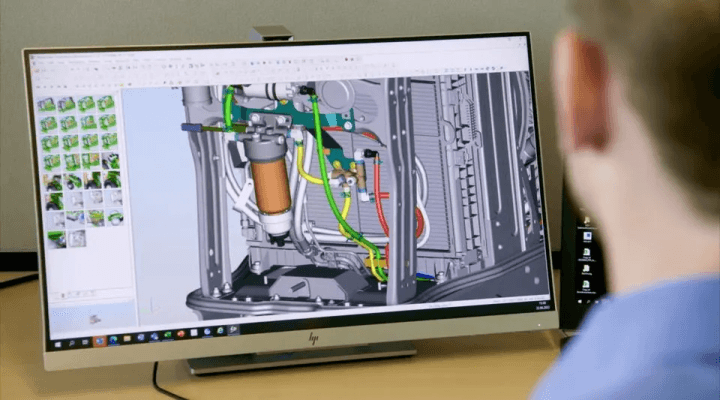
3D-printed parts at John Deere start as digital models. JOHN DEERE
- The agility afforded by 3D printing, allowing for faster and cheaper prototyping, aligns seamlessly with the Lean vision for a more digital and agile manufacturing process.
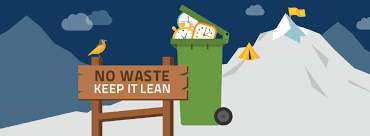